柳學義a,b,陳闖a.,b,楊艷宇a(中北大學a.材料科學與工程學院;b.山西省高分子復合材料工程技術研究中心,太原030051)
摘要:以硅橡膠為基體,T60導電炭黑為填料,制備了填充型硅橡膠復合材料。研究了炭黑填充量、硫化劑用量以及硫化時間對橡膠物理性能和導電性能的影響。結果表明:炭黑填充量、硫化劑用量以及硫化時間均會對橡膠的物理性能和導電性能產生影響。其中,炭黑填充量對橡膠的導電性能影響最為顯著。當炭黑用量為20份,硫化劑用量為7份,硫化時間為11 min時,所得橡膠的物理和導電性能最佳,拉伸強度為5.67 MPa,扯斷伸長率為133.1%,撕裂強度為16.9 kN/m,邵爾A硬度為81,體積電阻率為165Ω·cm。
關鍵詞:炭黑;導電橡膠;復合材料
中圖分類號:TM215;TQ333.93 文獻標志碼:A 文章編號:1009-9239(2012)01-0015-04
0·引言
導電橡膠是一種復合型導電高分子材料,具有柔韌性好、易加工以及導電、導熱等性能,在抗靜電、電磁屏蔽/吸波、導電、傳感等領域得到廣泛應用[1-4]。應用于導電橡膠的基體材料一般有硅橡膠、氟硅橡膠、氯丁膠、乙丙橡膠等[5]。與天然橡膠及其它合成有機橡膠相比,硅橡膠具有很高的熱穩(wěn)定性、較好的脫模性,并具有優(yōu)異的耐臭氧老化、氧老化、光老化和天候老化性能[6],成為應用最廣泛的導電橡膠材料。在制備通用型導電橡膠方面,由于炭黑價格便宜、對橡膠有補強作用并且可提高其耐候性和耐磨性,因此填充炭黑的導電硅橡膠綜合性能最好,應用最為廣泛[7]。在導電硅橡膠的需求量與日俱增的背景下,通過優(yōu)化出導電炭黑T60填充硅橡膠GY131的最佳工藝條件,進一步研究其性能,為應用于工業(yè)生產奠定堅實的基礎,具有重要的現實意義。
1·實驗
1.1主要原料
硅橡膠,型號:GY131,北京頂業(yè)工貿有限公司;導電炭黑,型號:T60,天津金秋實化工有限公司;鈦酸酯,工業(yè)級,天長市綠色化工助劑廠;過氧化二異丙苯,工業(yè)級,天津市東麗區(qū)天大化學試劑廠。
1.2主要設備與儀器
開放式煉膠機,型號:SK-160B,上海橡塑設備廠;平板硫化機,型號:XQLB-25D,上海第一橡膠機械廠;電子拉伸試驗機,型號:CMT6104,深圳三思材料檢測有限公司;橡膠邵氏硬度計,型號:XHS-W,營口市新興實驗機械廠;四探針電阻率測試儀,型號:SB120,上海乾峰電子儀器有限公司。
1.3試樣制備
將硅橡膠在雙輥開煉機上混煉,混煉均勻后將導電炭黑與鈦酸酯混合均勻一起加入橡膠中繼續(xù)混煉,混煉均勻后再加入硫化劑DCP,之后混煉一段時間出片。4 h后將膠料置于平板硫化機上進行硫化,硫化工藝為:溫度160℃,壓力150 MPa,時間10 min。
1.4性能測試
拉伸、撕裂性能:按ISO 37-2005進行測試;邵爾A型硬度:按GB/T 531.1-2008《橡膠邵爾A型硬度實驗方法》進行測試;體積電阻率(ρν)在室溫下進行測試;結果取5次測試的平均值。
2·結果與討論
2.1 T60用量對橡膠性能的影響
2.1.1 T60用量對橡膠物理性能的影響
表1為導電炭黑T60添加量對導電橡膠物理性能的影響。從表1可以看出,隨著導電炭黑T60用量的增加,邵爾A硬度逐漸增大,扯斷伸長率逐漸減小,拉伸強度和撕裂強度呈先增大后減小的趨勢,且在導電炭黑用量為20份時達到最大值。其原因主要是:導電炭黑在橡膠基體中起到補強作用,但過量的炭黑粒子會破壞橡膠基體的韌性,因此,橡膠的拉伸和撕裂強度呈先增大后減小的趨勢。
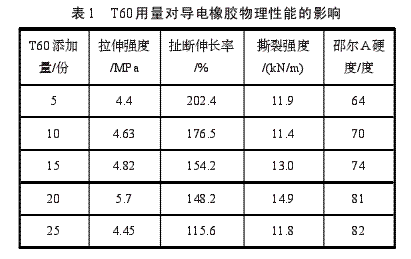
2.1.2 T60用量對橡膠導電性能的影響
圖1為導電炭黑T60用量對橡膠體積電阻率的影響。其中,當炭黑填充量為5份時,橡膠的體積電阻率為無窮大,基本處于絕緣狀態(tài),故未在圖中表示出來。從圖1可以看出,隨著導電炭黑T60用量的增加,橡膠的體積電阻率逐漸降低,且降低趨勢先大后小、先快后慢,最后趨于平緩。對于粒子填充型導電復合材料,導電性能一般分為絕緣區(qū)、逾滲區(qū)和導電區(qū)。逾滲區(qū)是指體系的導電性能發(fā)生突變的區(qū)域。從圖1可以看出,當導電炭黑添加量達到10份以后,橡膠的體積電阻率明顯下降,進入逾滲區(qū),當達到20份時,體系內部的導電網絡已基本形成,導電性能趨于平穩(wěn),繼續(xù)增加填料份數,橡膠的導電性能沒有較大改善。因此,20份為實驗的最佳用量。
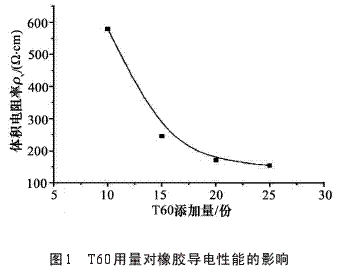
2.2硫化劑(DCP)用量對橡膠性能的影響
2.2.1硫化劑(DCP)用量對橡膠物理性能的影響
導電炭黑用量固定為20份,硫化劑(DCP)用量對導電橡膠物理性能的影響如表2所示。
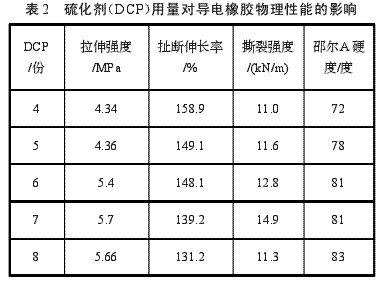
從表2可以看出,隨著硫化劑DCP用量的增加,橡膠的拉伸、撕裂、邵爾A硬度等力學性能都有不同程度的提高,在DCP用量為7~8份時達到最大,之后有下降趨勢。在橡膠硫化過程中,硫化劑的作用是將生橡膠的線型分子通過交聯反應,使之變成立體網絡狀結構的體型分子,從而提高橡膠的物理機械性能。但過量的硫化劑會造成橡膠的物理機械性能降低。當交聯程度過大時,交聯點間的相對分子質量減小,不利于鏈段的熱運動和應力傳遞,交聯結構易遭到破壞,造成應力集中,從而使拉伸強度下降。同時,交聯密度過大時,在外力作用下交聯網絡遭到破壞會造成裂紋沿缺陷發(fā)展,使撕裂強度下降。
2.2.2硫化劑用量對橡膠導電性能的影響
圖2為硫化劑用量對橡膠導電性能的影響。
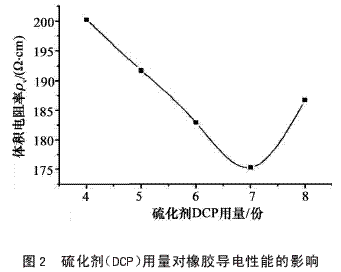
從圖2可以看出,隨著硫化劑用量的增加,橡膠的體積電阻率呈先降低后升高的趨勢。在橡膠硫化的過程中,隨著交聯密度的增加,導電網絡更加致密,炭黑也發(fā)生進一步運動,使得導電網絡更均勻,導電性增加。但隨著硫化劑用量的繼續(xù)增加,無規(guī)的交聯網絡隨之增加,阻礙了炭黑分子的進一步運動,破壞了導電網絡的結構,從而使橡膠導電性能下降;另外,炭黑是大量自由基的攜帶者,這些自由基是炭黑導體的載流子。作為硫化劑的DCP分解也會產生自由基,一部分被用來引發(fā)交聯反應,剩余的可與炭黑中的自由基在硫化溫度下結合,從而使橡膠基體中的載流子下降,降低了其導電性能。綜合考慮硫化劑用量對橡膠物理性能及導電性能的影響,7份為最佳的硫化劑用量。
2.3硫化時間對橡膠性能的影響
2.3.1硫化時間對橡膠物理性能的影響
在確定了炭黑填充量、硫化劑用量兩個因素后,研究了硫化時間對橡膠物理和導電性能的影響。表3為橡膠物理性能的測試結果。
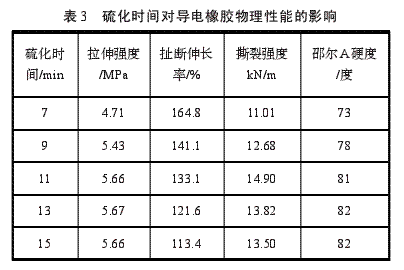
由表3可知,隨著硫化時間的延長,橡膠的拉伸、撕裂、邵爾A硬度等力學性能都有不同程度的提高,之后趨于穩(wěn)定,說明硫化時間的適當延長有助于完善橡膠內部的交聯網絡,橡膠的力學性能得到提高。但橡膠的撕裂強度呈先增加后降低的趨勢,這可能是因過密的交聯網絡阻礙了分子鏈的定向排列,加重了交聯鍵分布的不均勻性,致使應力分布更不均勻,使撕裂強度降低。
2.3.2硫化時間對橡膠導電性能的影響
圖3為硫化時間對橡膠導電性能的影響。

從圖3可以看出,硫化時間為7~11 min時,橡膠的體積電阻率下降明顯。在11~13 min達到最低值,之后略有上升。橡膠硫化過程中,隨著硫化時間的增加,橡膠內部的交聯網絡變得完善,炭黑粒子相互接觸的幾率增多,形成相互接觸的鏈狀導電通道,從而提高了橡膠的導電性能。但若硫化時間過長,會發(fā)生過硫化現象,破壞橡膠內部的導電網絡,使橡膠的導電性能降低。綜合考慮硫化時間對橡膠物理及導電性能的影響,11 min為最佳硫化時間。
3·結論
分析了炭黑填充量、硫化劑用量、硫化時間3個因素對導電硅橡膠物理和導電性能的影響。結果表明:3個因素均對橡膠的物理和導電性能產生影響。其中,炭黑填充量對橡膠的導電性能影響最為顯著。當炭黑用量為20份,硫化劑用量為7份,硫化時間為11 min時,橡膠的物理和導電性能達到最佳。橡膠的拉伸強度為5.67 MPa,扯斷伸長率為133.1%,撕裂強度為16.9 kN/m,邵爾A硬度為81,體積電阻率為165Ω·cm。
參考文獻:
[1]耿新玲,劉君,任玉柱,等.導電硅橡膠研究進展[J].航空材料學報,2006,26(3):283-288.
[2]黃英,李郁忠,周傳友,等.導電硅橡膠導電性和電熱性研究[J].橡膠工業(yè),2002,2(49):77-82.
[3]Ji Yunfeng,Chi Mingchan.Carbon Black-filled ImmiscibleBlends of Poly(vinylidene flouride)and High Density Poly-ethylene:Electrical Properties and Morphology[J].PolymerEngineering and Science,1998,38(10):1649-1657.
[4]郭巍,吳行,鄭振忠,等.導電炭黑/天然橡膠力學和導電性能研究[J].絕緣材料,2011,44(1):58-60,65.
[5]張洪雁,曹壽德,王景鶴.高性能橡膠密封材料[M].北京:化學工業(yè)出版社,2007.
[6]聶恒凱.橡膠材料與配方[M].北京:化學工業(yè)出版社,2004:31-38.
[7]趙麗瓊,李斌,丁紹煥.炭黑填充導電硅橡膠導電特性研究概況[J].有機硅材料,2011,25(2):117-120.